The cement manufacturing process
Nesher constantly tests and implements new methods and the use of recycled materials in order to optimize production processes in terms of the environmental footprint.
How was cement discovered?
Natural bonding materials were used as far back as the Roman Empire and even reached the land of Israel. From that period until the 19th century, cement was not used because people did not know how to produce it artificially.
The first man-made cement was created in 1824 by Joseph Aspdin, an English builder from Leeds and changed the face of history.
Aspdin discovered that a mixture of clay soil and limestone, roasted in a fire kiln at an extremely high temperature, creates a new material he called "Portland Cement" due to its color, which reminded him of the Portland soils in the south of England.
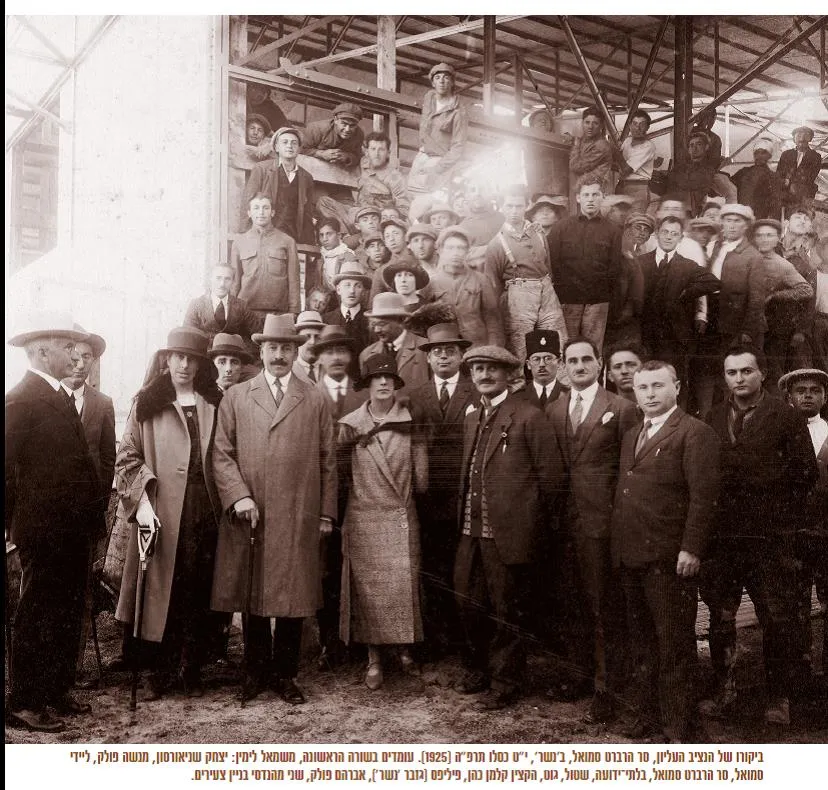
How is cement prepared?
Cement is the product of heating a mixture containing mainly limestone and clay to very high temperatures, then mixing the product with additional materials (gypsum, limestone and more) and grinding it into a fine powder.
The limestone is quarried from the plant's quarry, which is located about three kilometers from the plant. The stone is transported by a conveyor belt to the plant, where it is mixed with clay to obtain a uniform mixture, which is important for the stability of the production process and the uniformity of the final product.
The mixing process takes place in a dedicated facility, without using water in order to save water and reduce energy consumption.
The raw materials mixture is then grinded to a fine powder, combined with additional materials, whose purpose is to achieve precision of the chemical composition required for the production process.
After grinding, the raw materials are fed to the furnace through preheating towers, where residual energy from the production process is used to heat them.
This is how energy savings are achieved in the process, optimizing it environmentally. At the high temperatures in the furnace (about 1600 degrees Celsius), the raw mixture turns into a new material called clinker, which gives the cement and concrete their strength since it hardens when it comes in contact with water.
We increasingly use alternative (waste-based) fuels in the clinker production process, thereby replacing some of the fossil fuels.
The clinker is mixed with additional materials (gypsum, limestone, coal ash and others, depending on the type of cement produced) and grinded into a fine gray powder.
Most of the cement is kept in storage tanks (silos) and marketed in bulk (in dedicated sealed cement tanks), and some is marketed in bags.